Prior to inspection, the Pacific InterWest team visits the project location to document all Exterior Elevated Elements subject to SB721/SB326 requirements. With this information, our team establishes a baseline number of elevated elements to inspect in compliance with these requirements. The selection process for the elevated elements to be inspected is random, however measures are taken to ensure the sampling reflects a true measure of the condition of all elevated elements at the subject property. At this same time, PIW evaluates and determines if lead paint or asbestos is present and notifies the Client if abatement measures are required.
A turnkey approach to managing SB721 and SB326 compliance
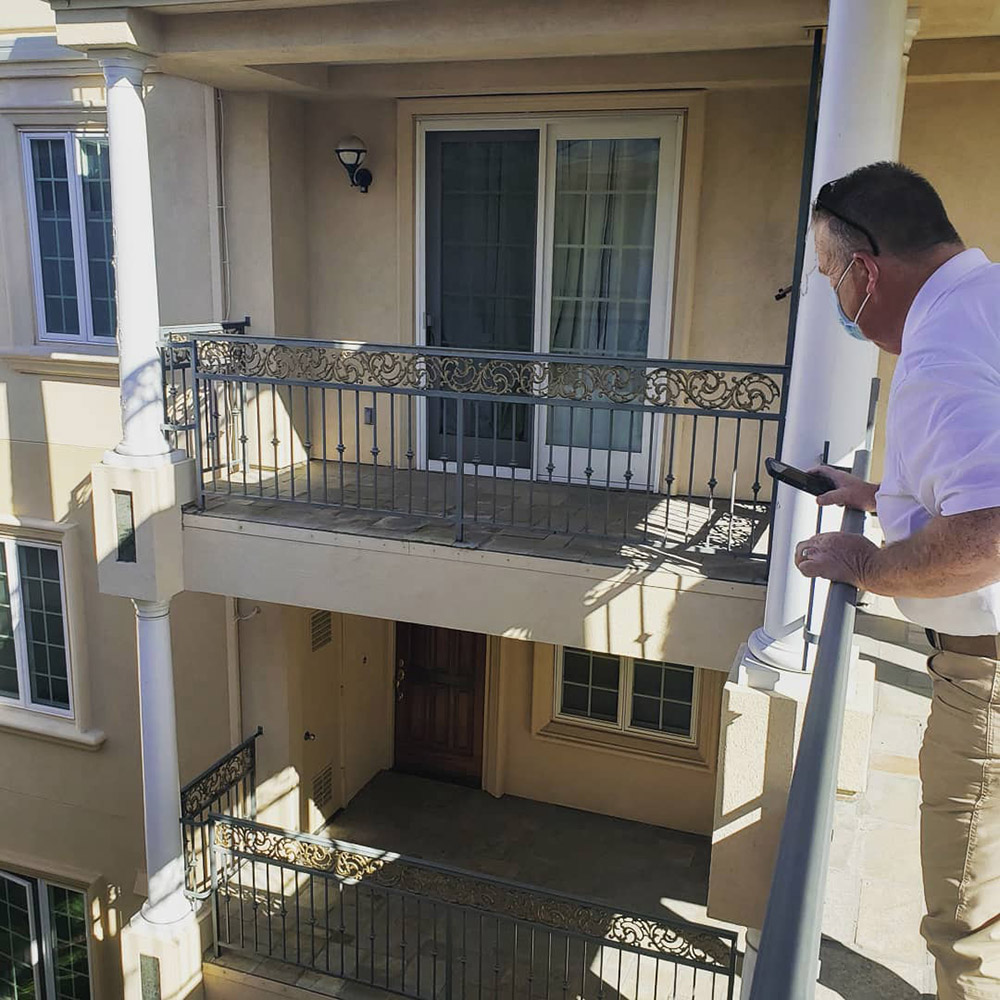
The purpose of the inspection is to determine if the Exterior Elevated Elements and associated waterproofing components are in a generally safe condition, adequate working order, and free from any hazardous condition caused by fungus, deterioration, decay, or improper alteration to the extent that the safety or welfare of the public or the occupants are endangered. The law requires inspection of associated waterproofing components that protect the load-bearing elements including sheet metal flashings, membranes, coatings, sealants, and features that may penetrate the membrane such as guardrail attachments, drains, and scuppers. Load-bearing components are those components that extend beyond the exterior walls of the building to deliver structural loads from the element to the building.
Our professional inspection team consists of an ICC-certified building inspector and one or more technicians. The team members wear company-issued uniforms with readily visible Pacific InterWest identification badges. Arrangements with the Client’s property management team are made prior to and for these site visits.
If the Element is open decking – PIW performs a visual inspection of the element surface, supporting structure and guardrail attachments using a wood probe and moisture meter.
If the bottom of the Element is covered with wood or stucco there are three options on how to perform the inspection:
- PIW can drill a series of small holes (approximately 1” in diameter) through the finish material on the bottom side of each of the Elements. Through these holes PIW inserts a borescope to view and photograph the condition of the supporting structure of the Element. After the inspection has been completed the holes can be patched and painted. This option provides no future ventilation and requires that new holes be drilled in subsequent SB721/SB326 inspections.
- PIW can drill a series of holes (approximately 2″ in diameter) through the finish material on the bottom side of each of the Elements. Through these holes PIW inserts a borescope to view and photograph the condition of the supporting structure of the element. After the inspection has been completed PIW installs a two-inch-round “puck” style vent. This provides beneficial ventilation and much easier access in subsequent SB721/SB326 inspections.
- PIW can cut a slot through the finish material on the bottom side of each of the Elements at the inboard an outboard side of the element. Through these slots PIW inserts a borescope to view and photograph the condition of the supporting structure of the Element. PIW installs a removable strip vent when the inspection is complete. This method, which provides both ventilation and ease of access in subsequent inspections, is often preferred when the buildings are clad with wood or when there are long Elements such as walkways.
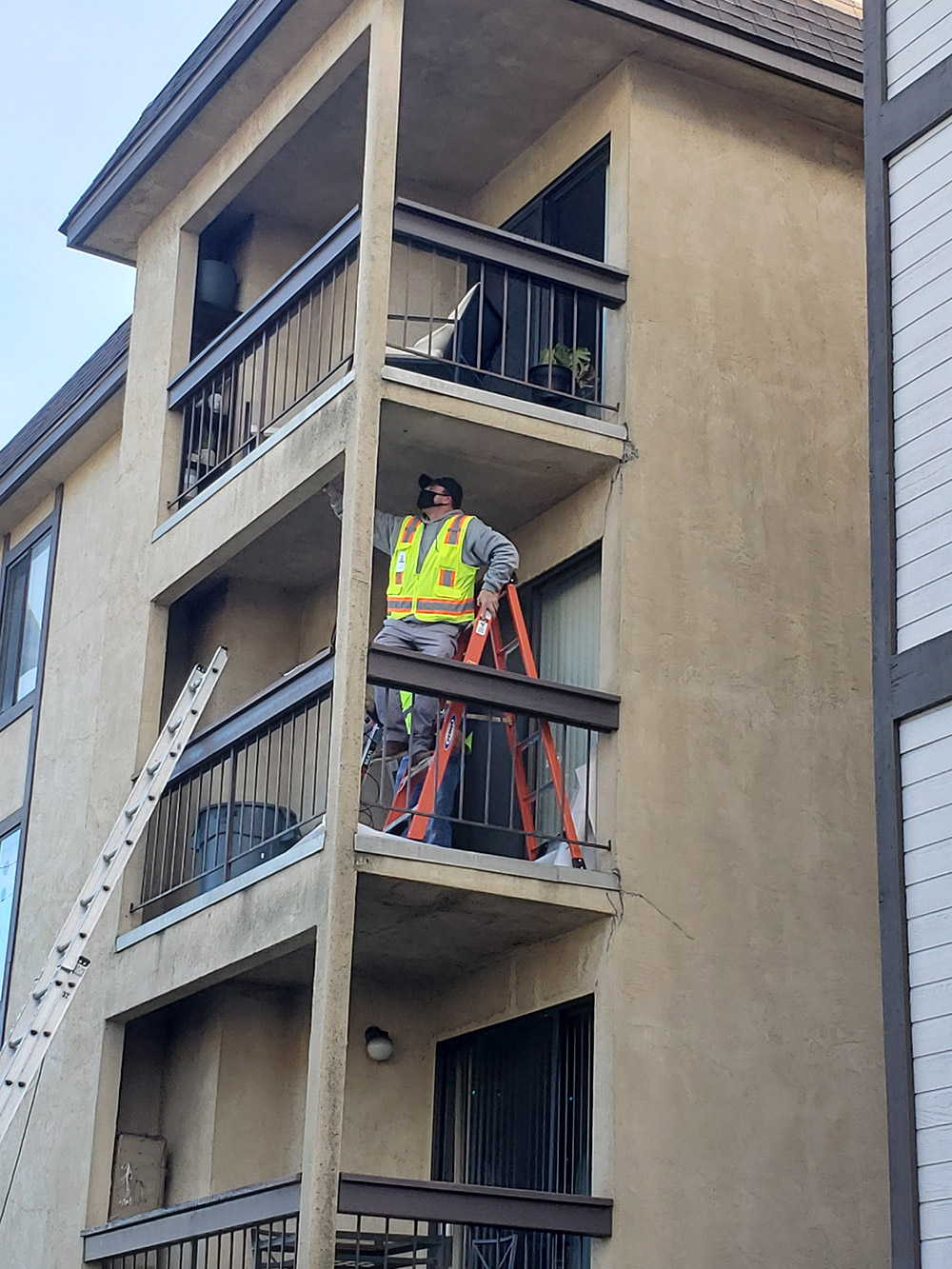
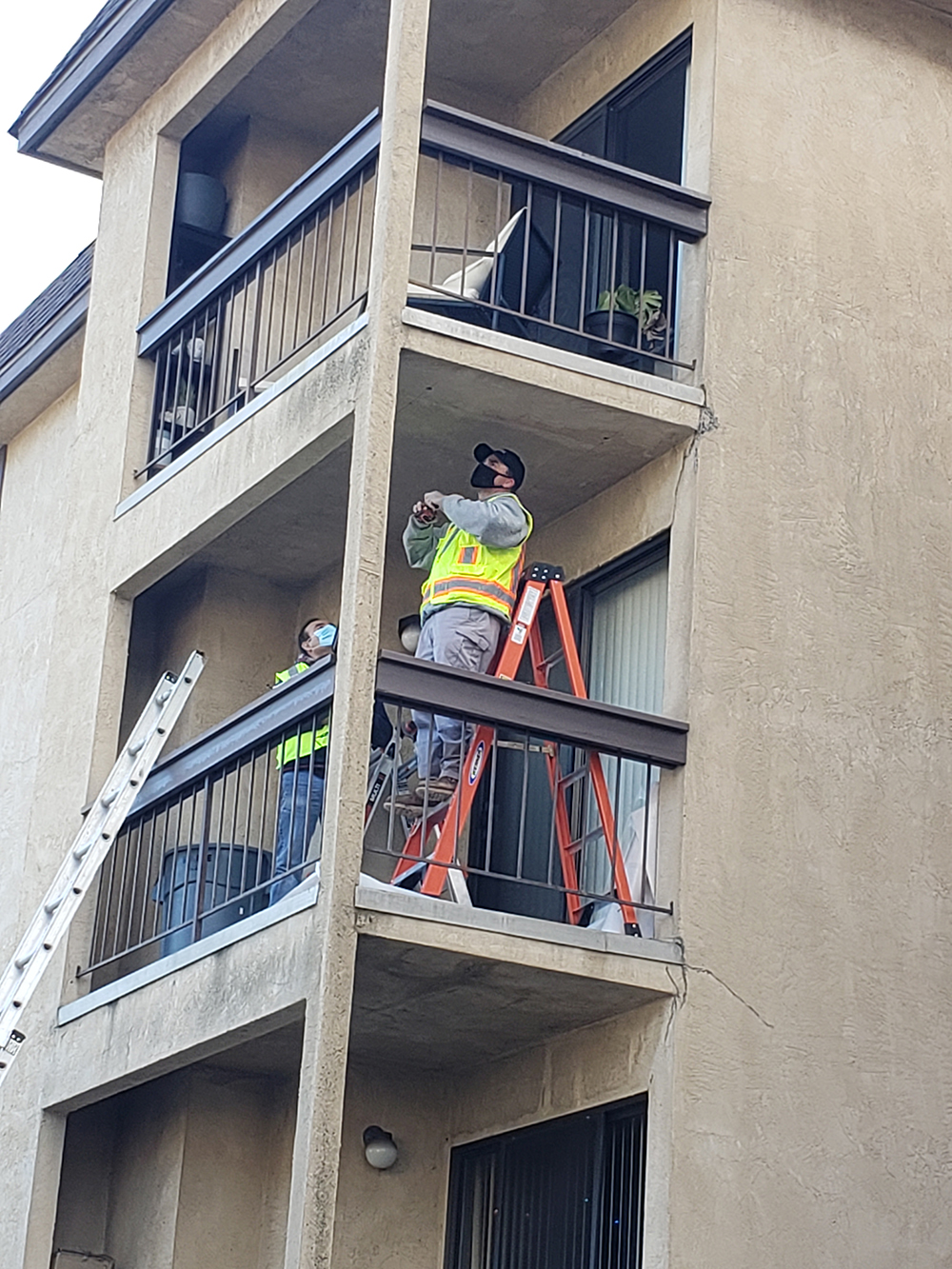
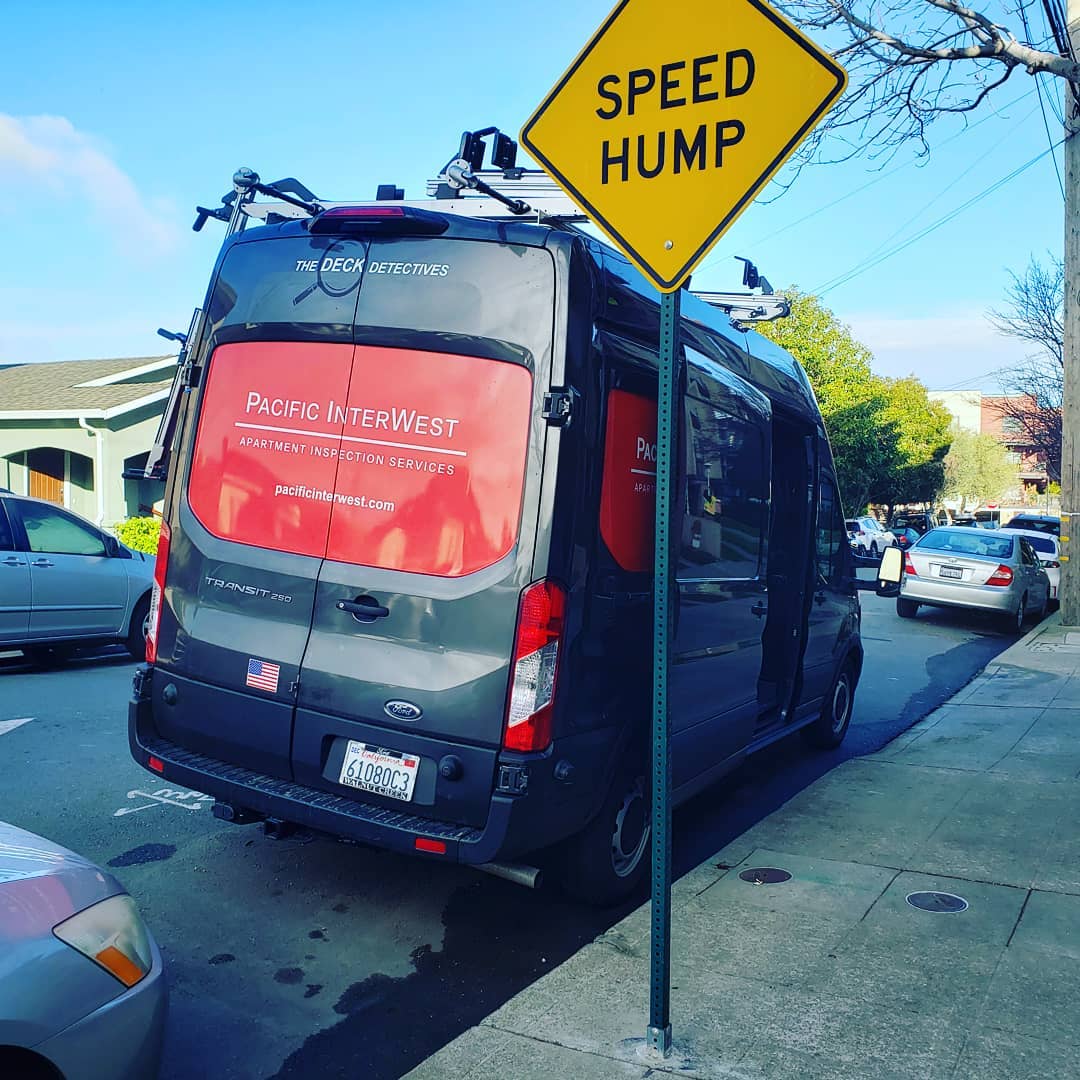
Pacific InterWest records the findings of each individual element inspection through PIW QTECH®, our proprietary online inspection software. PIW will provide the findings of these inspections in what we call a Tier 1 report. This report shall include an executive summary of the findings for the property, the matrix of all Elements in the property and dates that the Elements were inspected. Photographs shall be taken and included in the report. Reporting is issued to the Client and the municipal authority as required. As required by SB721/SB326, PIW shall provide an estimate of “expectations of future performance and projected service life” of each of the Elements.
Should the initial investigation (Tier 1) reveal conditions that require additional inspection, PIW will remove exterior materials to determine both the cause and extent of the damage. This additional investigation is called a Tier 2 inspection and may include a possible evaluation by a structural engineer if warranted. This inspection is only completed with the Client’s authorization to proceed. If a Tier 2 investigation is deemed necessary by PIW, it must be completed in order to finalize the SB721/SB326 inspection, however, the Client may wish to schedule this work for a later date.
If an elevated element is determined to be an immediate threat to the safety of the public, the Pacific InterWest team contacts the building owner immediately to notify them of the need to restrict access to the element.
A report is issued to the client following completion of Tier 1 and Tier 2, if applicable, inspections. These reports are provided and distributed in strict compliance with the requirements of SB721 and SB326. Included in these reports are the results of the Tier 1 and Tier 2 inspections, a determination of the cause of any damage if present, a remaining serviceable life of the element and waterproofing, and scheduling of the next cycle of inspections.
Please contact us for sample inspection reports.
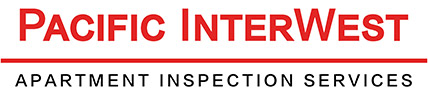